the current state of recycling
As an example, due to the collapse of a recycling company recently, Australia has a stockpile of 12,500 tonnes of soft plastic awaiting export to Southeast Asia for disposal. The Cyclion plant offers an eco-friendly alternative, efficiently converting this waste into 2 million litres of diesel fuel, equivalent to fueling around 33,000 cars, while minimising harmful emissions and costs associated with traditional waste-to-energy methods.
%20(2).webp)
the solution
Cyclion technology
%20(1).webp)
How I explain Green Chemistry to my friends
The Washing Machine
The Cyclion process is revolutionary, employing "Green Chemistry" as an environmentally friendly method of liquefaction to convert plastic and biomass waste into oil, all at low temperature and pressure. This oil can be refined into fuels or electricity.
This process has similarities with doing your washing. Visualise a washing machine: you toss in clothes, detergent, and a few cycles later, the dirt is gone and you get clean clothes. Likewise, the Cyclion process treats municipal waste through their special detergent (the green chemistry) and cycles of ‘washing’ until it's reusable and in a form that can be converted to fuel and electricity, just like laundry that is dried and ironed.
step 01
No more sifting through the rubbish
Just as separating red socks from white shirts is crucial, current methods of waste management also hinges on initial sorting starting at the home—precisely classifying plastics, biomass, and more before processing. This operation is both costly and labor-intensive.
Cyclion revolutionises this expensive and labour-intensive practice by dumping the waste straight into the machine -without the need to sort- to begin the washing process.
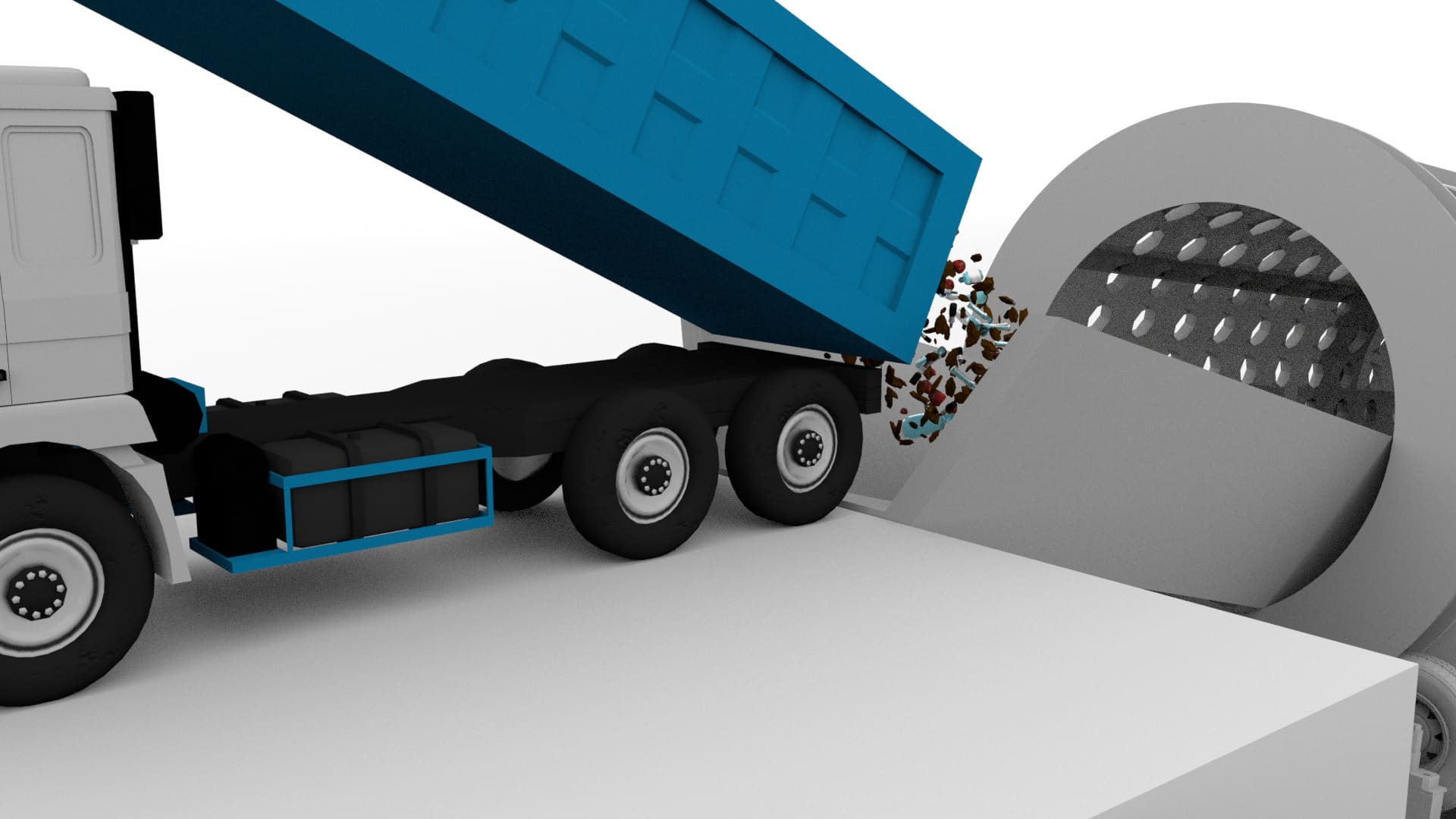
The garbage truck arrives at the cyclion plant, dumping all rubbish into the system.
step 02
Wash until it’s clean
Like a pre-wash detergent tackles clothing stains, Cyclion's green catalysts are added to liquify the plastic bags that contain household waste. This unveils the food scraps, soft plastics, hard plastics, and glass within.
The machine then runs through various cycles, each with variations on the liquifying catalysts. Each cycle the waste is liquified and degraded until what is left in the tank is inorganic matter, the solid glass or metals, that can be separated and recovered.
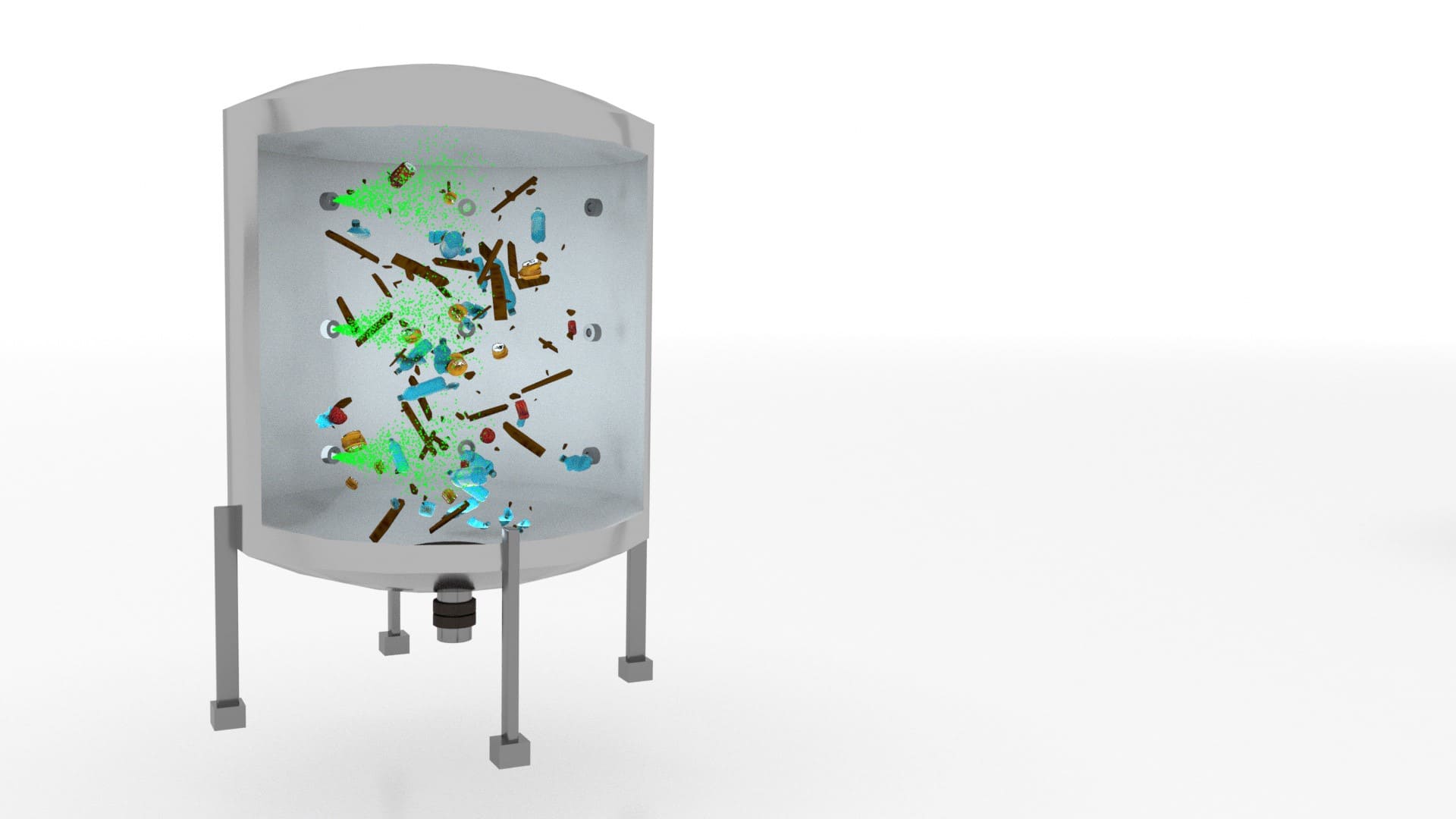
Liquification vessel. Environmentally green catalysts are added to the rubbish.
step 03
Use it, store it, sell it
What’s been degraded becomes an oil that can then be further processed into fuel or converted into a flammable gas to generate electricity. A waste to resource opportunity that can remove the waste burden of nations and deliver economic growth and capability to produce resources locally.
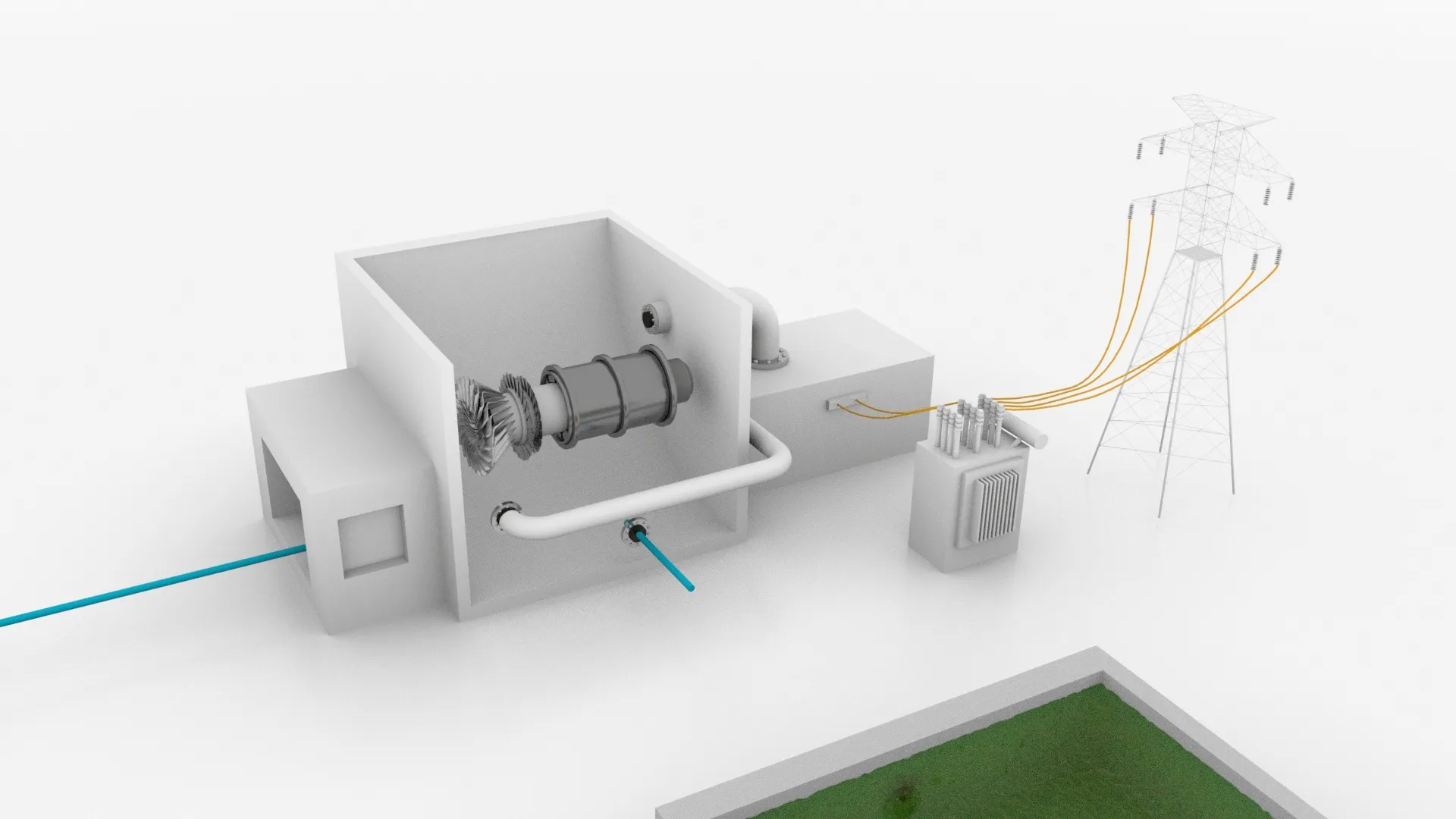
A fully operational Cyclion plant could scale up in excess of 1000 tonne per day, producing more than 52 million litres of diesel per annum.
Future focused
Reinventing the wash
The waste degradation process itself isn't novel, yet Cyclion’s innovation lies in:
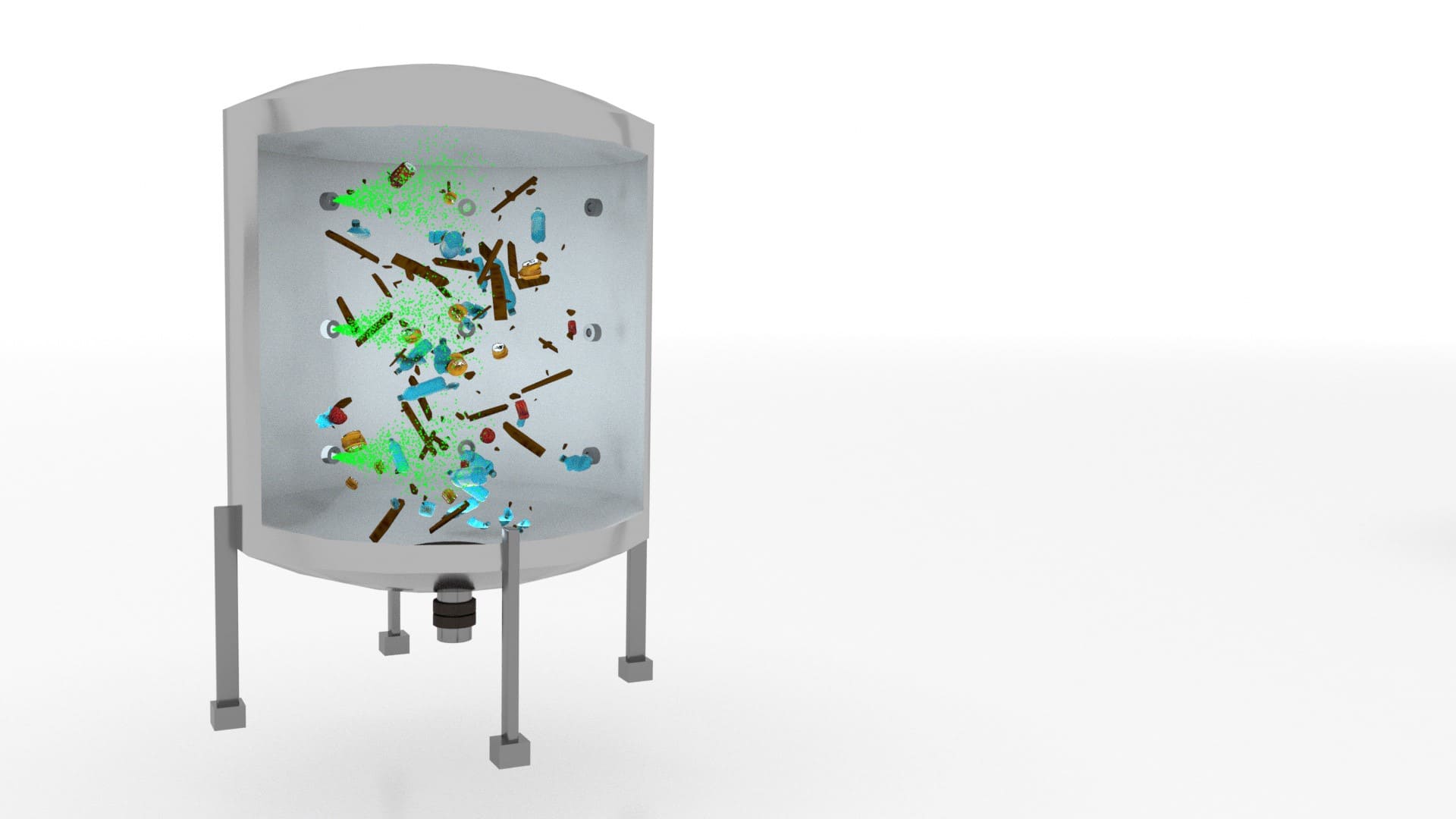
Green catalysts
A.k.a. our patent-pending environmentally friendly detergent mix
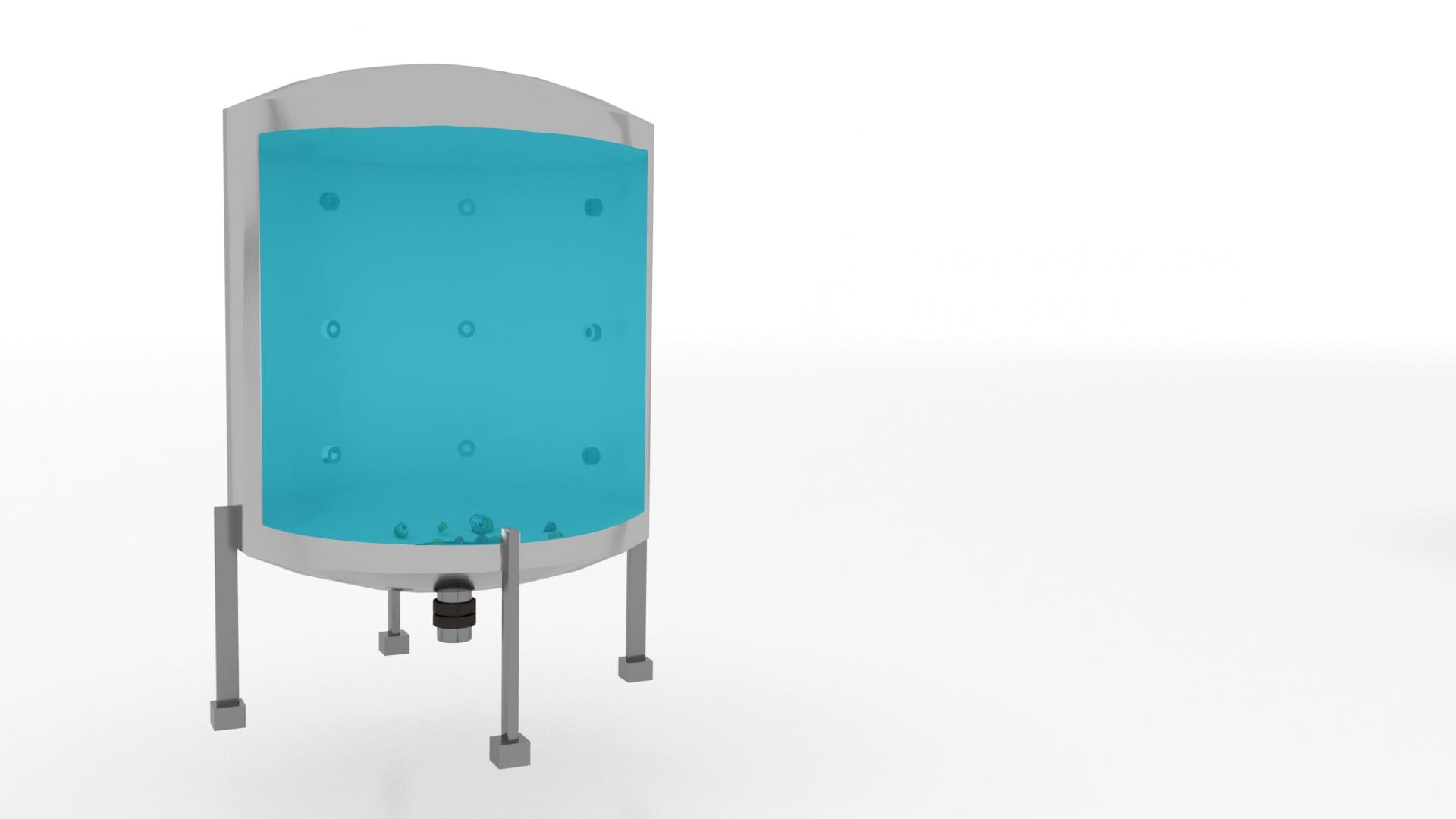
Low operating temperature
Less than 310°C resulting in almost carbon neutral process
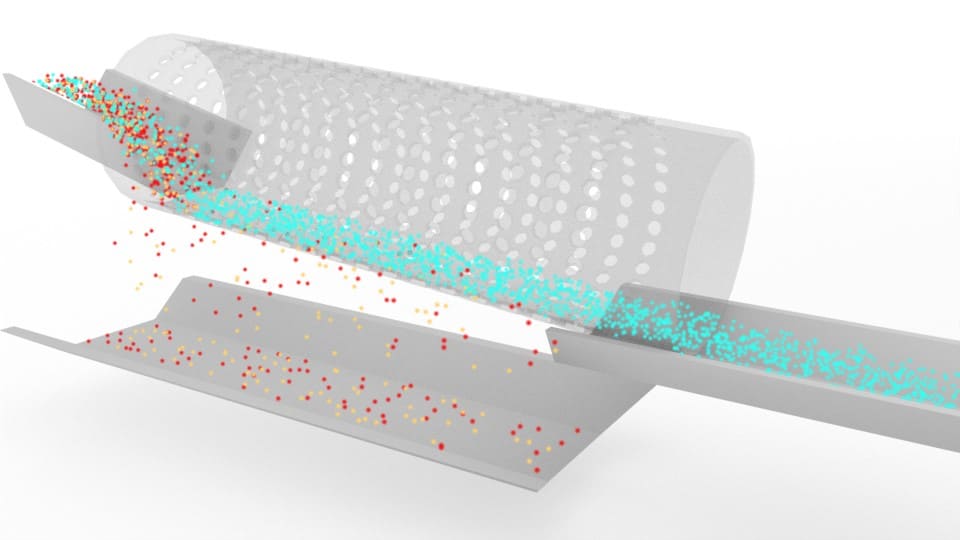
minimal pre-sorting reqUIRED
Reducing the labor and cost traditionally spent on sorting
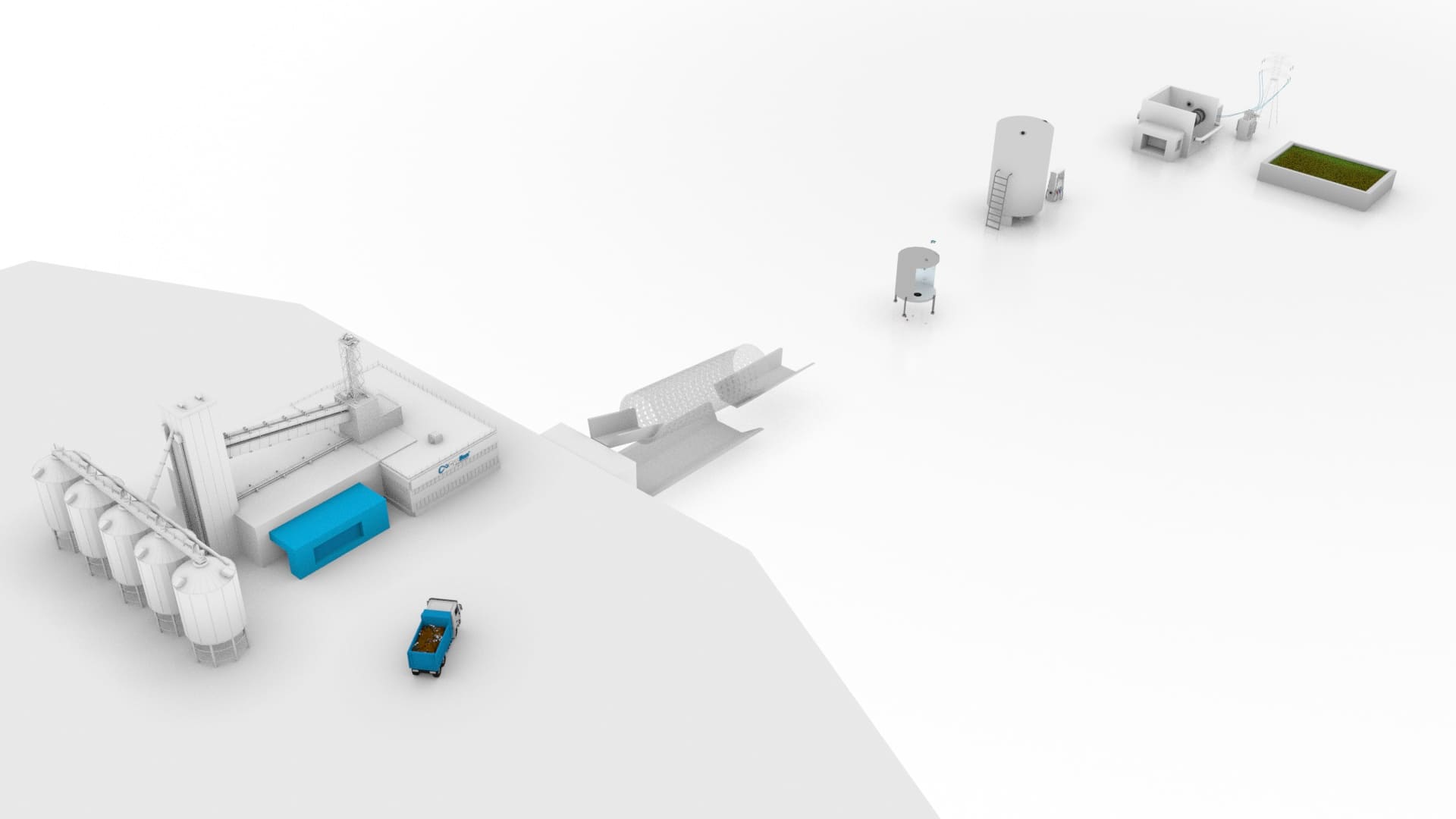
modular and mobile
Adaptable to some of the world’s hardest to reach places
How do we stack up?
Cyclion vs Current Waste Management Methods
Pyrolysis
Incineration/
gasification
CYCLION
MINIMAL Pre-sorting
Often requires pre-treated rubbish in the form of refuse derived fuel or pretreatment.₁
Often requires preparation in the form of refuse derived fuel (RDF) for incinerators and similar for gasification.₁
All waste can be safely processed together. Saving significant expense and time when compared with other recycling and waste management methods.
LESS THAN 310ºC OPERATING TEMP
The likelihood of dioxin and furan production increases dramatically over 400ºC. Pyrolysis typically operates at around 400-700ºC.
Compared with the average of around 500°C for pyrolysis, or around 800°C for incineration, or between 800-1500 for gasification.
Operates at less than 310°C temperature
Modular & Scaleable SYSTEM
Despite having been around for decades, pyrolysis has had limited commercial application in Australia.
Large scale and complex - typically costs hundreds of millions of dollars. Is complex to establish and run.
1 Alfè, M., Gargiulo, V., Porto, M., Migliaccio, R., Le Pera, A., Sellaro, M., Pellegrino, C., Abe, A. A., Urciuolo, M., Caputo, P., Calandra, P., Loise, V., Rossi, C. O., & Ruoppolo, G. (2022). Pyrolysis and Gasification of a Real Refuse-Derived Fuel (RDF): The Potential Use of the Products under a Circular Economy Vision. Molecules, 27(23). https://doi.org/10.3390/molecules27238114
The Cyclion plant offers an eco-friendly alternative, efficiently converting this waste into 2 million liters of diesel fuel, equivalent to fueling around 33,000 cars, while minimising harmful emissions and costs associated with traditional waste-to-energy methods.